TUDA
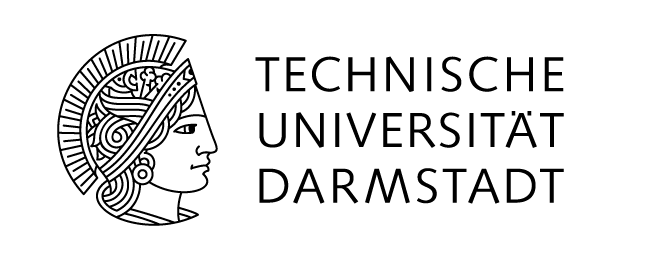
The Institute of Energy Systems and Technology at the Technical University of Darmstadt has large experience in the field of power plant technology, particularly in solid fuel combustion processes and related CO2 capture techniques. Its key expertise lies in modeling and simulation of multiphase flows (e.g. coal-fired boilers, mills, cyclones), modeling of heat exchanger systems (e.g. HRSG), steady-state and dynamic simulation of power plant processes, and experimental investigations of solid fuel combustion processes in laboratory and pilot scale test facilities. A 1 MWth pilot plant consisting of two interconnected Circulating Fluidized Bed (CFB) reactors has been erected and operated to investigate the carbonate and chemical looping technologies in semi-industrial scale.
In recent research projects, the plant was upgraded to be operated as High-Temperature Winkler® gasifier. Furthermore, it has been extended with syngas cleaning equipment as well as a synthesis test rig. Preliminary tests can be carried out in a laboratory reactor to determine the optimum process conditions. The Advanced process models including 1D reactor models have been developed for various processes. A highly sophisticated in-house CFD code using the discrete element method (DEM) for particle/particle interaction has been developed and validated for detailed 3D simulations of dense gas/particle flows. Advanced reaction models for solid fuel conversion, gas phase kinetics, radiative transfer etc. have been implemented into CFD codes for efficient simulations of solid fuel combustion devices.
ROLE in Bio-MeGaFuel
The Technical University of Darmstadt is investigating two processes High-Temperature Winkler® (HTW®) Gasification and Chemical Looping Gasification, in the flexible pilot plant. Various aspects of gasification, gas cleaning, and biomethanol synthesis are being studied in laboratory and pilot-scale setups.
In the pilot-scale experiments at the Technical University of Darmstadt the influence of different fluidizing media, long-term effects (such as the accumulation of ash in the bed material and potential effects on agglomeration or fouling) and the gas cleaning are being closely examined. Together with project partners, numerous aspects of the process chain are being investigated in multi-week test campaigns. The results are used to create simulations and compare the two processes, HTW® Gasification and Chemical Looping Gasification, in terms of their economic viability and sustainability.